Airbus Atlantic is a major aeronautical supplier, a 100% subsidiary of Airbus, which aims to meet the highest standards of quality and operational excellence, with flexibility and agility. The Industry R&D department must optimize quality, speed and costs. To do this, sharing feedback and standardizing best practices is crucial. This makes it possible to speed up complex projects, reduce costs and optimize quality.
What are the challenges of manufacturing?
Frédéric Laborderie is a manufacturing engineer. He is responsible for industrialization in Rochefort and manages the implementation of two projects impacting the entire A350 aircraft. Indeed, as part of the launch of the A350 Freighter and the A350 ULR (Ultra Long Range), which will allow 24-hour flights for the Australian airline Qantas, Frédéric is making changes to manufacturing processes, processes, and resources, which have an impact on their site in Rochefort and on the landing gear box manufacturing line.
The team is multidisciplinary, and generates numerous exchanges with their design office, their customer, their manufacturing, production, logistics chain or even the steering committee. This approach allowed them to find solutions and implement these two modifications without impacting their current chain for the production of 350 passenger train cases, which has been in production for several years.
In this context, Airbus Atlantic carries out failure mode and criticality analyses (PFMEA in English) Frédéric needed to quickly get feedback on the use of these means that are not currently used on this chain.
Questions to get a REX
In this context, Frédéric Laborderie asks a question to his peers via the Ask Airbus Atlantic platform to quickly obtain feedback on the use of certain means necessary for these two modifications.
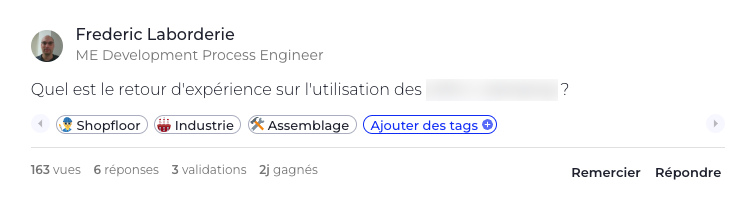
He adds tags that give the context in which he is looking for feedback. The platform's AI thus notifies the most relevant colleagues. He thus quickly obtains feedback from two colleagues who are relevant to implement this specific method. Having this implementation constraint, it was necessary to anticipate possible failures, and to avoid known dysfunctions from occurring as part of the modifications.
Asking questions in a quality approach
This approach makes it possible to anticipate potential problems and malfunctions, to optimize the costs and quality of production, as well as to maximize the efficiency of the processes. For example, it could have been a question of planning the parts, spares and backups necessary to avoid any stoppage or malfunction in the production line: this makes it possible to reduce costs by avoiding losses of time and the additional costs associated with solving problems that could have been avoided thanks to the analysis of feedback. The answers quickly made it possible to see that there was no no-go, no known defects, in the use of the method mentioned.
Save and save time
The use of the platform allowed Frédéric Laborderie to save several days to obtain the feedback necessary for the implementation of the two projects. Without the platform, you would have had to set up meetings, send emails, before finding the right person. Using the platform allowed him to quickly obtain clear and precise answers, without wasting time. It is a quality, cost avoidance and planning approach: the three pillars of their modification treatments.